Panoval Label S.A. ก่อตั้งขึ้นครั้งแรกในปี 1991 ที่ประเทศสวิตเซอร์แลนด์ โดยอาศัยจุดแข็งของบริษัทในตะวันออกไกล Panoval (Asia) จึงก่อตั้งขึ้นในนครโฮจิมินห์ ประเทศเวียดนาม ในปี 2017 โรงงานที่ทันสมัยแห่งนี้สร้างขึ้นเพื่อวัตถุประสงค์เฉพาะ โดยมีสายการเคลือบหลายสายและห้องปลอดเชื้อที่ได้รับการรับรองมาตรฐาน ISO Class 6 สำหรับผลิตภัณฑ์ระดับไฮเอนด์ที่ต้องใช้เทคโนโลยีการเคลือบล่าสุด นอกจากนี้ บริษัทยังได้รับการรับรองมาตรฐาน ISO 14644-2 อีกด้วย
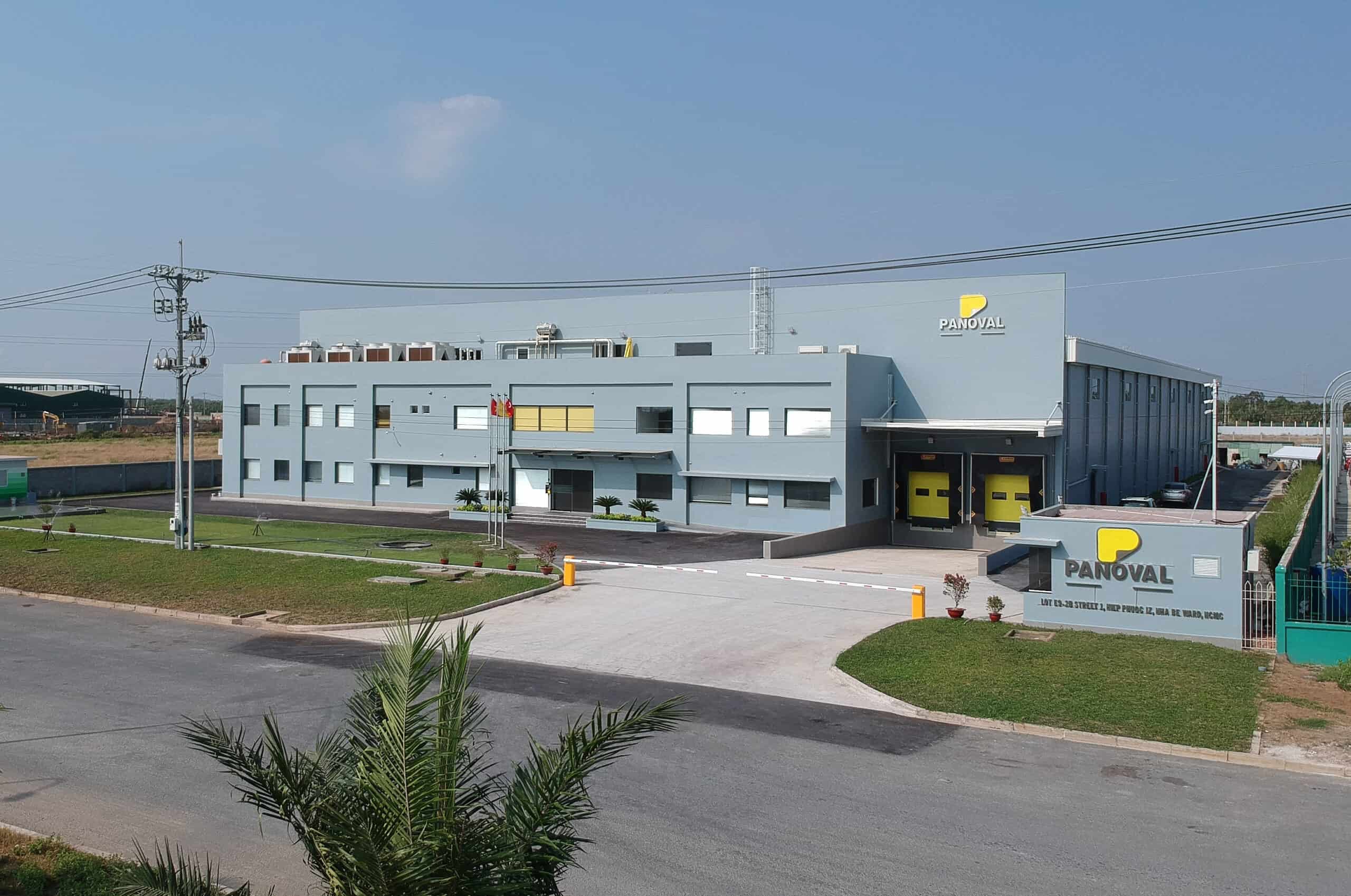
ฉลากกาวไวต่อแรงกดมากกว่า 60% ของปริมาณการผลิตทั่วโลกผลิตขึ้นในตะวันออกไกล ซึ่งรวมถึงฉลากสำหรับใช้งานด้านอิเล็กทรอนิกส์ การแพทย์ และเภสัชกรรม นี่คือเหตุผลหลักที่บริษัทก่อตั้งขึ้นในเวียดนาม แม้ว่าโดยรวมแล้วบริษัทจะยังคงเป็นเจ้าของในยุโรปก็ตาม แม้จะมีโรงงานผลิตเพียงแห่งเดียว แต่ Panoval ก็ยังทำงานร่วมกับตัวแทนจำหน่ายและลูกค้าโดยตรงในระดับนานาชาติ และได้สร้างธุรกิจที่มีสาขาอยู่ทั่วโลก ความคล่องตัวในการผลิตและชื่อเสียงด้านความยืดหยุ่นทำให้พวกเขาได้กลายมาเป็นซัพพลายเออร์ชั้นนำของสต็อกฉลากเฉพาะทางที่ไม่ได้มาตรฐาน ลูกค้าทั่วไปคือตัวแทนจำหน่ายบรรจุภัณฑ์แบบยืดหยุ่น ผู้แปลงฉลาก และเครื่องพิมพ์ทั่วไป
ปัจจุบัน Panoval มีพนักงาน 25 คนและกำลังขยายตัวอย่างต่อเนื่อง ทีมผู้บริหารประกอบด้วยผู้เชี่ยวชาญที่มีประสบการณ์ยาวนานและปฏิบัติงานในระดับนานาชาติซึ่งมีประสบการณ์มากมายในการพัฒนาและผลิตแผ่นลามิเนตสำหรับติดฉลากสำหรับการใช้งานที่ต้องการความแม่นยำสูง Wilco van Zwieten กรรมการบริษัทเข้าร่วม Panoval ในตำแหน่งผู้จัดการฝ่ายขายในปี 1993 และปัจจุบันเป็นส่วนสำคัญของทีมดังกล่าว หน้าที่ของเขาคือการขับเคลื่อนธุรกิจใหม่ และเขามองว่าความก้าวหน้าทางเทคโนโลยีและนวัตกรรมเป็นปัจจัยสำคัญต่อความสำเร็จของบริษัท ดังที่เขาอธิบายไว้ว่า “ในตลาดที่มีการแข่งขันสูงเช่นนี้ ขนาดของบริษัทที่ค่อนข้างเล็กและการดำเนินงานของสายการเคลือบสองสายที่แตกต่างกันมากทำให้เราประสบความสำเร็จได้มาก นอกเหนือจากงานกระแสหลักที่มีปริมาณงานสูงที่เราทำแล้ว ทีมงานฝ่ายผลิตของเรายังสามารถทำงานเฉพาะทางเล็กๆ อีกหลายงาน ซึ่งบางครั้งต้องเปลี่ยนผลิตภัณฑ์สามหรือสี่ครั้งในหนึ่งกะ เราใช้เทคโนโลยีหลอมร้อนด้วยแสงยูวีล่าสุดเพื่อสำรองระบบที่ใช้ยางเป็นฐาน เทคโนโลยีแสงยูวีนี้เป็นเทคโนโลยีเดียวที่มีศักยภาพในการทดแทนการเคลือบที่ใช้ตัวทำละลายได้… ไม่ใช่ทันที แต่ภายในสิบถึงสิบห้าปี หากต้องการทำเช่นนี้ คุณต้องมีโซลูชันการบ่มด้วยแสงยูวีระดับสูงสุดพร้อมคุณสมบัติครบครันที่สนับสนุนเทคโนโลยีดังกล่าว และนั่นคือสิ่งที่เราออกแบบร่วมกับผู้ผลิตเครื่องจักรและ GEW เพื่อให้เราสามารถตอบสนองความต้องการทั้งหมดของเราในอีกห้าถึงสิบปีข้างหน้าได้ เรามีความพร้อมสำหรับอนาคต”
ระบบบ่มด้วยแสงยูวีที่ออกแบบและผลิตในสหราชอาณาจักรโดย GEW ของ Panoval ประกอบด้วยหัวหลอด NUVA2 จำนวน 5 หัว ซึ่งสามารถรองรับหัวหลอดได้สูงสุด 7 หัว โดยติดตั้งไว้กับลูกกลิ้งเย็นขนาด Ø1000 มม. บนสายการเคลือบของ Sung An Machinery (SAM) หลอดไฟติดตั้งไว้รอบดรัมบนชุดโครงแข็งซึ่งแยกจากชุดลูกกลิ้งและเลื่อนออกจากตำแหน่งที่ยึดไว้บนราง ทำให้เข้าถึงพื้นผิวลูกกลิ้งและด้านล่างของชุดหัวหลอดได้

เมื่อเริ่มค้นหาโซลูชันบ่มด้วยแสงยูวี ฟาน ซวิเอเตนได้รับการแนะนำให้ติดต่อ GEW โดยเพื่อนร่วมงานชาวมาเลเซียซึ่งเพิ่งทำงานร่วมกับ GEW ในการออกแบบและติดตั้งระบบบ่มด้วยแสงยูวีสำหรับการใช้งานเคลือบแบบปลดปล่อย ฟาน ซวิเอเตนเล่าว่า “ผมไปเยี่ยมชมโรงงานในมาเลเซียเพื่อดูการติดตั้งด้วยตัวเอง จากนั้นจึงเริ่มพูดคุยกับ GEW ในตอนแรก เราคุยกันช้าๆ เพราะเรารู้ว่าเราต้องการโซลูชันที่ซับซ้อนและได้รับการออกแบบทางวิศวกรรมพร้อมการปรับแต่งในระดับสูง” แรงผลักดันค่อยๆ เพิ่มขึ้นเรื่อยๆ เมื่อเขาทำงานตามข้อกำหนดของ Panoval กับแผนก ‘Specialist UV‘ ของ GEW เขากล่าวว่า “เราประทับใจกับบุคลากรของ GEW มาก พวกเขาตอบสนองรวดเร็วและตอบคำถามของเราได้หมดทุกข้อ แม้ว่าจะเป็นเรื่องเทคนิคก็ตาม การทำงานกับบุคลากรที่เหมาะสมเป็นสิ่งสำคัญที่สุด”
จากนั้น Van Zwieten ได้ไปเยี่ยมชมโรงงานผลิตของ GEW ในสหราชอาณาจักรระหว่างการสร้างระบบ ซึ่งทำให้ทั้งสองฝ่ายมีโอกาสหารือเกี่ยวกับระบบในรายละเอียดเพิ่มเติม และเพื่อให้แน่ใจว่าระบบเป็นไปตามข้อกำหนดและความคาดหวังทั้งหมด สำหรับการออกแบบ การติดตั้ง และการสนับสนุนทางเทคนิคอย่างต่อเนื่องสำหรับระบบนั้น Van Zwieten เปิดเผยอย่างตรงไปตรงมาว่า “กระบวนการทั้งหมดราบรื่น เราไม่มีปัญหาใดๆ เลย หากเกิดปัญหาทางเทคนิคขึ้น เราจะมีระบบตรวจสอบระยะไกลของ GEW เพื่อช่วยเหลือเรา แต่เรามีประสบการณ์ที่ดีจริงๆ กับระบบนี้” เขากล่าวต่อว่า “จนถึงปัจจุบัน ความต้องการเดียวที่เรามีต่อบริการตรวจสอบระยะไกลคือรายงานรายสัปดาห์ที่เราได้รับโดยอัตโนมัติ ซึ่งแสดงข้อมูลการจัดการที่มีประโยชน์ เช่น เวลาการทำงาน ชั่วโมงการทำงานของหลอดไฟ การใช้พลังงาน และประสิทธิภาพ นอกจากนี้ยังทำให้เราอุ่นใจได้ เพราะเรารู้ว่าหากเกิดปัญหาขึ้น แพลตฟอร์มตรวจสอบจะแจ้งปัญหาทันที”
ดังที่ van Zwieten ชี้ให้เห็น ค่าใช้จ่ายทั้งหมดได้รับการประหยัดในการกำหนดคุณลักษณะของระบบบ่มด้วยแสงยูวีใหม่ เพื่อให้แน่ใจว่าจะตอบสนองความต้องการทุกประการในอีกหลายปีข้างหน้า เขาให้ความเห็นว่า “เครื่องเคลือบทั่วไปจะติดตั้งหลอดไฟหนึ่งหรือสองหลอดแล้วก็จะพอใจ เรามีความแตกต่างในเรื่องนี้โดยติดตั้งหลอดไฟห้าหลอดพร้อมกัน ซึ่งหมายความว่าเราสามารถปรับระยะห่างระหว่างการใช้สารเคมีและการบ่มจากงานหนึ่งไปยังงานถัดไปได้ ทำให้เราสามารถรองรับตลาดที่แตกต่างกันมากมายที่ไม่สามารถรองรับได้ด้วยเทคโนโลยีนี้ในปัจจุบัน นี่คือเหตุผลที่เราเลือกที่จะทำงานร่วมกับบุคลากรของ GEW พวกเขามีความเชี่ยวชาญทางเทคนิคและประสบการณ์สำหรับระบบที่ซับซ้อนเช่นนี้ ขณะนี้ เรามุ่งหวังที่จะได้รับผลตอบแทนจากการลงทุนอย่างรวดเร็วด้วยการประหยัดพลังงานและงานใหม่ที่ระบบ UV นำมาให้เรา”
ตลาดเป้าหมายของ Panoval คืออุตสาหกรรมยาและอิเล็กทรอนิกส์ ซึ่งต้องการฉลากที่สะอาดกว่าและมีคุณสมบัติการปล่อยก๊าซตกค้างที่ต่ำกว่า Van Zwieten อธิบายว่า “การปล่อยก๊าซตกค้างเป็นกรณีที่ผลิตภัณฑ์ยังคงปล่อยก๊าซออกมาหลังจากการผลิต ซึ่งอาจเป็นปัญหาที่ร้ายแรงสำหรับผู้ผลิต ตัวอย่างเช่น ในโลกของอิเล็กทรอนิกส์ การปล่อยก๊าซอาจทำให้ระบบอิเล็กทรอนิกส์ขัดข้องได้ และหากคุณกำลังผลิตสินค้าราคาแพง เช่น ไดรฟ์ออปติคัล ปัจจัยความล้มเหลวใดๆ จะต้องลดลงให้น้อยที่สุด หากไม่สามารถกำจัดได้หมดสิ้น” เขากล่าวต่อว่า “นี่คือจุดที่ระบบการบ่มด้วยแสงยูวีทำให้เราแตกต่างอย่างแท้จริง เราได้ทดลองและทดสอบกระบวนการบ่มในสภาพแวดล้อมการผลิตห้องปลอดเชื้อ ISO 6 แล้ว และเราสามารถผลิตแผ่นลามิเนตที่มีคุณสมบัติการปล่อยก๊าซตกค้างต่ำกว่ามาก ซึ่งทำให้เราสามารถเสนอผลิตภัณฑ์ที่สะอาดกว่าและเหนือกว่ามากให้กับผู้ผลิตเฉพาะทางเหล่านี้และผู้แปรรูปของพวกเขา”
ด้วยระบบ UV เฉพาะที่ออกแบบมาโดยเฉพาะสำหรับ Panoval สามารถควบคุมระยะห่างระหว่างหัวเคลือบและหลอดไฟบ่มได้อย่างแม่นยำ ซึ่งหมายความว่าสามารถได้รับแสงที่เหมาะสมที่สุดสำหรับการใช้งานที่หลากหลาย นอกจากนี้ ระบบ UV ยังได้รับการออกแบบด้วยตัวเรือนหลอดไฟ 7 ชิ้นและตลับหลอดไฟที่ปรับเปลี่ยนได้ 5 ชุด ซึ่งหมายความว่าสามารถวางหลอดไฟในตำแหน่งต่างๆ ได้หลายตำแหน่งเพื่อควบคุมระยะเวลาการบ่มได้อย่างมีประสิทธิภาพ การเพิ่มระยะเวลาตั้งแต่การใช้สารเคมีกับพื้นผิวจนถึงจุดที่สารเคมีได้รับการบ่ม จะช่วยให้มีเวลามากขึ้นในการระบายก๊าซที่ไม่ต้องการก่อนการเคลือบ นอกจากนี้ยังส่งผลต่อความเร็วในการทำงานของเครื่องอีกด้วย ช่วงเวลาการปลดปล่อยก๊าซที่ยาวนานขึ้นทำให้สามารถบ่มได้อย่างมีประสิทธิภาพและปลอดภัยด้วยความเร็วในการทำงานที่เร็วขึ้นถึง 50% ดังที่ van Zwieten กล่าวว่า “สิ่งนี้ทำให้เรามีข้อได้เปรียบในการแข่งขันเหนือบริษัทในสหรัฐฯ และยุโรปหลายแห่งที่จำกัดให้ทำงานด้วยความเร็วที่ช้ากว่า”
เพื่อแสดงให้เห็นถึงความมุ่งมั่นของบริษัทในการแสวงหาโซลูชันที่สมบูรณ์แบบ Panoval ยังได้ลงทุนติดตั้งเซ็นเซอร์ตรวจวัด UV หลายจุด (mUVm) ของ GEW จำนวน 5 ตัวเข้ากับหัวหลอด UV แต่ละหัว และเชื่อมต่อกับระบบ ERP เซ็นเซอร์เหล่านี้สามารถวัดได้ที่ตำแหน่งตรงกลางของหลอด และที่ขอบสุดของแผ่นใยยาว 500 มม. และ 1,050 มม. นอกจากการอ่านค่ามิเตอร์อนุภาคซึ่งวัดระดับการปล่อยก๊าซได้อย่างแม่นยำทันทีหลังจากการบ่มแล้ว mUVm ยังช่วยให้ทีมงานผลิตสามารถวัดและตรวจยืนยันว่าได้ให้ปริมาณและความเข้มข้นของ UV ในระดับที่ถูกต้องตลอดกระบวนการผลิตหรือไม่ ด้วย mUVm คุณสามารถสร้างใบรับรองการบ่มด้วย UV สำหรับทุกชุดได้โดยบันทึกเอาต์พุต UV แบบเรียลไทม์สำหรับทุกหลอด ข้อมูลเอาต์พุต UV แบบเรียลไทม์จะถูกส่งออกผ่านอินเทอร์เฟซ RESTful API
อย่างไรก็ตาม เป้าหมายของ van Zwieten คือการพัฒนาประโยชน์ของระบบตรวจวัด UV ต่อไปโดยใช้ความสามารถในการรายงานเพื่อค้นคว้าและกำหนดระดับพลังงานที่เหมาะสมสำหรับการยึดเกาะ การยึดเกาะ และการปลดปล่อยผลิตภัณฑ์หลักของบริษัท ข้อมูลเซ็นเซอร์ UV นี้จะนำไปใช้สร้างแผนที่การบ่มแบบ 3 มิติของผลิตภัณฑ์ม้วนใหญ่ทุกม้วน ซึ่งจะช่วยให้ผู้ผลิตปลายทางสามารถตรวจสอบย้อนกลับได้ในระดับสูง แม้ว่าข้อมูลนี้จะมีความสำคัญอย่างยิ่งต่อลูกค้าในอุตสาหกรรมยา อิเล็กทรอนิกส์ และอวกาศ แต่ก็สามารถใช้ในการตั้งค่าการผลิตซ้ำได้อย่างรวดเร็วและมีประสิทธิภาพเช่นกัน
ทีมงานของ Wilco van Zwieten ยังต้องเอาชนะความยากลำบากทางเทคนิคที่เกิดจากสภาพแวดล้อมในนครโฮจิมินห์อีกด้วย อากาศ 18,000 ม3/ชม. ที่ใช้ในการทำความเย็นจะถูกดูดเข้ามาในห้องปลอดเชื้อจากภายนอกอาคารที่อุณหภูมิโดยรอบประมาณ 35°C พวกเขาได้ติดตั้งระบบกรองสองขั้นตอนและท่อทางเข้าเพิ่มเติมอีกประมาณ 25 เมตรเพื่อลดอุณหภูมิของอากาศ ความชื้น และอนุภาคปนเปื้อนใดๆ ภายใน ก่อนที่จะไปถึงหัวโคมไฟ
ทีมงานฝ่ายผลิตทั้งหมดขับเคลื่อนด้วยแนวคิดบุกเบิก โดยเน้นที่การใช้การวิจัยและพัฒนาเพื่อสร้างผลิตภัณฑ์ที่มอบข้อได้เปรียบทางการค้าให้กับผู้ใช้ปลายทาง ตัวอย่างเช่น การผลิตสารตั้งต้นสำหรับฉลากยางโดยใช้กระบวนการหลอมร้อนด้วยแสงยูวีที่ผ่านการปรับปรุง ดังที่ van Zwieten อธิบายไว้ว่า “เราจะไม่ใช้กาวร้อนแบบธรรมดาสำหรับฉลากยาง เนื่องจากกาวชนิดนี้ไม่เสถียร โดยเฉพาะอย่างยิ่งเมื่อมีน้ำหนักมาก ส่งผลให้ผู้แปรรูปต้องลดความเร็วในการแปรรูป เนื่องจากใบมีดตัดแม่พิมพ์จะปนเปื้อนกาวได้อย่างรวดเร็ว ในทางกลับกัน เราได้ปรับปรุงกระบวนการกาวร้อน UV ให้สมบูรณ์แบบขึ้น โดยเราสามารถบ่มกาวให้แห้งเล็กน้อยเพื่อสร้างกาวที่มีความเหนียวต่ำซึ่งมีการยึดเกาะขั้นสุดท้ายสูงมาก ซึ่งหมายความว่าผู้แปรรูปสามารถผลิตฉลากได้เร็วขึ้นและสะอาดขึ้นมาก นี่คือสถานการณ์ที่ทั้งสองฝ่ายได้ประโยชน์”
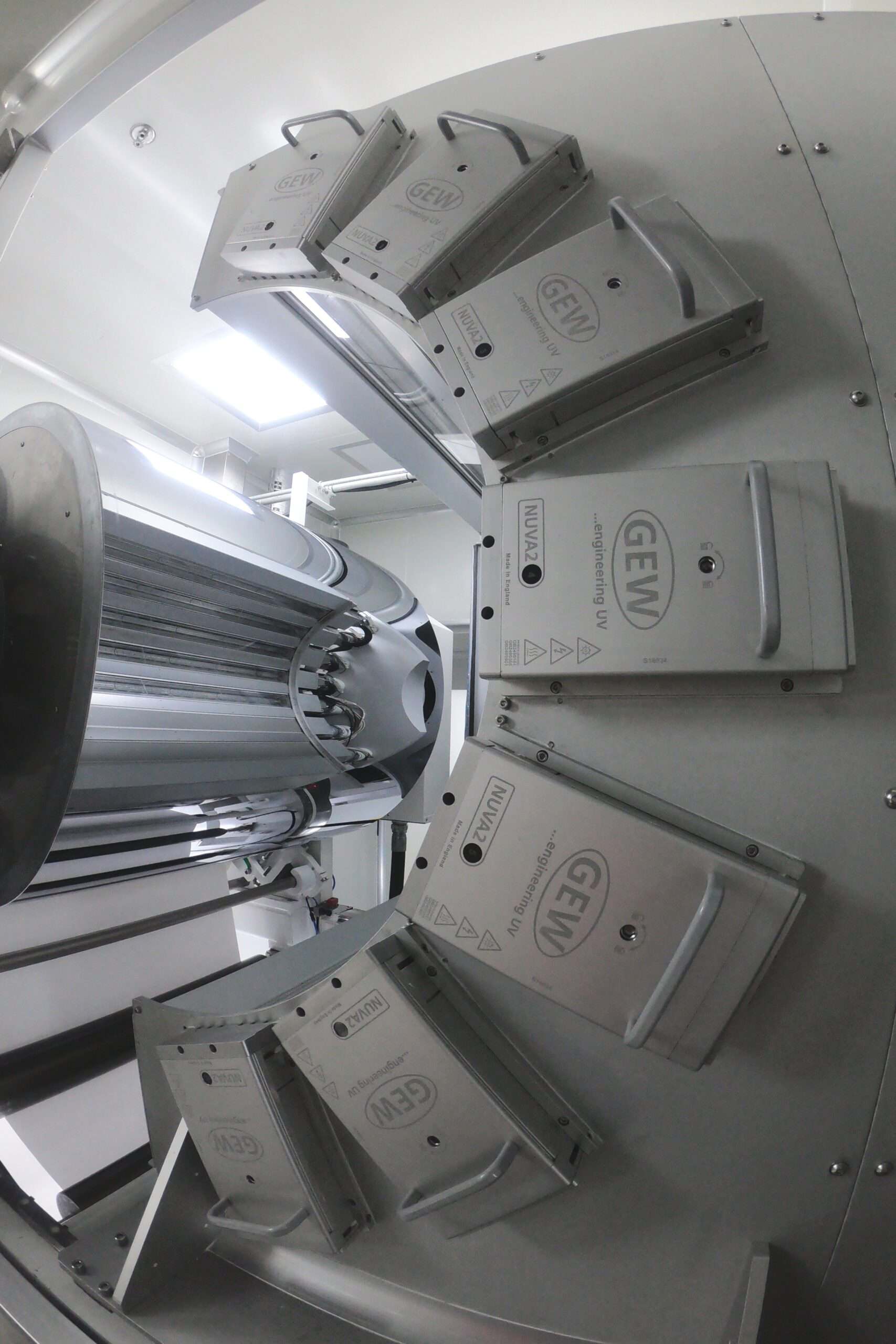
ข้อดีเชิงพาณิชย์ที่เกิดขึ้นจากขั้นตอนการผลิตทำให้ผลิตภัณฑ์ UV ของพวกเขาแตกต่างจากผลิตภัณฑ์ทั่วไป และช่วยชดเชยต้นทุนวัตถุดิบที่สูงกว่าเล็กน้อยจาก UV ได้ นอกจากนี้ van Zwieten ยังชี้ให้เห็นถึงแนวโน้มของตลาดที่ส่งผลดีต่อพวกเขาด้วย “ผู้ผลิตสารเคลือบจำนวนมากขึ้นเรื่อยๆ ผลิตโพลีเมอร์จาก UV และเราเห็นว่าราคาลดลงอย่างรวดเร็ว… ราคาลดลงไปแล้วกว่า 40% ในช่วงสามปีที่ผ่านมา เป็นเพียงเรื่องของเวลาเท่านั้นก่อนที่ UV จะเข้ามามีบทบาท”
ระบบหลอดไฟห้าหลอดของ Panoval ทำให้ทีมงานสามารถปรับกระบวนการอบให้เหมาะกับงานแต่ละงานได้ เพื่อให้อบทั้งก่อนและหลังได้ตามต้องการ ดังที่ van Zwieten อธิบายไว้ว่า “สำหรับงานบางประเภท เราจำเป็นต้องอบให้แห้งก่อน ซึ่งสามารถทำได้โดยใช้หลอดไฟเพียงหลอดเดียวที่ปลายทางเดิน ข้อดีของวิธีนี้คือทำให้ทางเดินยาวขึ้นถึง 130 ซม. และช่วยให้มีเวลาให้ก๊าซระเหยออกมาได้ก่อนที่สารเคลือบจะไปถึงสถานี UV ดังนั้นเราจึงสามารถผลิตฉลากสำหรับการใช้งานทางการแพทย์ที่มีความต้องการสูงได้ เช่น โดยไม่ต้องทำให้สายการผลิตสารเคลือบของเราช้าลง”
เพื่อวัดการเพิ่มขึ้นของความเร็วในแง่ของข้อได้เปรียบในการแข่งขัน ฟาน ซวีเทนกล่าวต่อว่า “เราสามารถทำงานเฉพาะเหล่านี้ได้เร็วถึง 40 เมตรต่อนาที ซึ่งสูงกว่ามาตรฐานสำหรับผลิตภัณฑ์เฉพาะประเภทนี้มาก โดยทั่วไปในยุโรปและสหรัฐอเมริกา จะทำงานที่ 25 เมตรต่อนาที และด้วยเหตุนี้ จึงทำให้ผลิตภัณฑ์ที่คล้ายกันมีราคาแพงกว่าอย่างเห็นได้ชัด”

การติดฉลากสำหรับการใช้งานทางการแพทย์มักจำเป็นสำหรับวัสดุที่ไม่ทอ ซึ่งดูดซับรังสีได้มากกว่าโพลีเอสเตอร์และโพลีโพรพิลีนมาก ซึ่งหมายความว่าต้องใช้กำลังในการบ่มด้วยแสงยูวีสูงเป็นประจำ และการบ่มเกินสามารถทำได้ง่ายด้วยกำลังไฟฟ้ายูวีสูงถึง 108 กิโลวัตต์ การบ่มเกินด้วยแสงยูวีใช้เพื่อเลียนแบบคุณสมบัติที่ต้องการมากขึ้นของกาวที่ใช้ตัวทำละลาย โดยเคลือบจะถูกบ่มให้มีความเหนียวน้อยและแห้งเมื่อสัมผัส แต่ในขณะเดียวกัน กาวก็ยังคงมีความเหนียวแน่นสูงและมีอายุการใช้งานยาวนาน กระบวนการนี้มีข้อดีอื่นๆ อีกด้วย ดังที่ van Zwieten อธิบายไว้ว่า “แรงยึดติดเริ่มต้นนั้นต่ำและยังช่วยให้ปรับตำแหน่งใหม่ได้ แต่การยึดติดขั้นสุดท้ายนั้นแข็งแรงมาก – เกิน 50 นิวตันอย่างง่ายดาย – ซึ่งจำเป็นสำหรับการติดฉลากประสิทธิภาพสูง จากนั้นเราจะกลับมาดูข้อดีในการแปลงสภาพ ซึ่งจะกลายเป็นกระบวนการที่รวดเร็วกว่ามากด้วยการเคลือบที่บ่มด้วยแสงยูวี” เขาสรุปว่า “เราสามารถได้รับประโยชน์ทั้งหมดของการเคลือบที่ใช้ตัวทำละลาย แต่ไม่มีการระเหยของก๊าซและสารที่สกัดได้ ซึ่งเป็นปัญหาสำหรับอุตสาหกรรมการแพทย์ อวกาศ และอิเล็กทรอนิกส์”
นอกจากนี้ Panoval ยังมีหน้าต่างควอตซ์ GEW ‘HiC’ ติดตั้งไว้กับหัวหลอด UV ซึ่งเหมาะเป็นพิเศษสำหรับการใช้งานหลอมร้อน ควอตซ์เกรดพิเศษนี้ช่วยให้พลังงาน UVC ผ่านไปยังสารเคลือบได้มากขึ้นเมื่อเทียบกับควอตซ์ทั่วไป ดังที่ van Zwieten แสดงความคิดเห็นว่า “เราไม่ได้ตัดมุมใดๆ ในการกำหนดคุณลักษณะของระบบ UV ของเรา และเรายังไม่เคยพบงานที่ระบบทำไม่ได้ เนื่องจากเราทำงานที่ต้องใช้ระยะเวลาสั้นและซับซ้อนหลากหลายประเภท เราจึงต้องมั่นใจว่าเราจะสามารถบรรลุสิ่งที่เราต้องการได้เสมอ และหากเราพบว่าต้องการพลังงานเพิ่ม เราก็สามารถเพิ่มตลับหลอด UV อีกสองตลับเข้าไปในตัวเรือนที่ว่างเปล่าได้อย่างง่ายดาย” เขาเสริมว่า “อย่างไรก็ตาม จากสถานการณ์ปัจจุบัน เราสามารถพิมพ์ฉลากด้วยความเร็ว 220 เมตรต่อนาทีได้ เรากำลังบรรลุความเร็วการผลิตที่เร็วกว่าการพิมพ์ด้วยตัวทำละลายแบบเดียวกันถึงสองเท่า ตัวอย่างเช่น เมื่อไม่นานนี้ เราได้ผลิตฉลากโพลีเอสเตอร์แบบถอดออกได้ที่มีแผ่นซิลิโคนปลดปล่อยตัวในปริมาณน้อยที่ความเร็ว 100 เมตรต่อนาที โดยมีน้ำหนักเคลือบที่เบา และไม่มีการระเหยของก๊าซเลย… และเท่าที่ฉันทราบ นั่นถือเป็นสถิติโลกใหม่”
“ระบบ GEW ประสบความสำเร็จตามที่เราต้องการอย่างแท้จริง ระบบนี้อบเกินและอบไม่ครบได้อย่างสมบูรณ์แบบ เราประหยัดการใช้ไฟฟ้าได้มหาศาลและลดปริมาณการปล่อยคาร์บอน ลองนึกภาพว่าระบบน้ำแบบเก่าของเราต้องใช้เตาอบเกือบ 40 เมตรที่อุ่นถึง 200 องศาเพื่อเอาน้ำออก… เราใช้พลังงานประมาณ 1,800 กิโลวัตต์ต่อชั่วโมง สำหรับสารเคลือบแบบน้ำ น้ำประมาณ 40% ของทุกกิโลกรัมจะต้องถูกสกัดออกมา ตอนนี้ด้วย UV เราสามารถทำงานได้ 220 เมตรต่อนาที และสูงสุดที่เราใช้คือประมาณ 600 กิโลวัตต์ต่อชั่วโมง ดังนั้นจึงเท่ากับหนึ่งในสาม”
อย่างไรก็ตาม ยังมีข้อควรพิจารณาอื่นๆ ที่ต้องคำนึงถึงเมื่อนำกระบวนการอบด้วย UV มาใช้ ดังที่ van Zwieten ชี้ให้เห็นว่า: ‘คุณต้องมีเจ้าหน้าที่ที่ได้รับการฝึกฝนและทุ่มเทมากกว่านี้เพื่อทำงานร่วมกับ UV และเข้าใจ และคุณต้องมีอุปกรณ์ที่ดีกว่านี้ตั้งแต่เริ่มต้น เมื่อเปรียบเทียบกันแล้ว เครื่องเคลือบที่ใช้ตัวทำละลายมีมากกว่า 1,100 เครื่องในประเทศจีนเพียงประเทศเดียว และเป็นเครื่องพื้นฐานราคาถูกที่ใช้งานง่าย ไม่จำเป็นต้องมีห้องทดลอง แต่เครื่องนี้เป็นอันตราย เนื่องจากมีพิษและก่อมลพิษ และยังสิ้นเปลืองพลังงานมาก” เมื่อเปรียบเทียบกับข้อดีของ UV เขาสรุปว่า “ด้วย UV คุณไม่จำเป็นต้องใช้เครื่องเผาขยะ ไม่เป็นพิษ ไม่เสี่ยงต่อการเกิดไฟไหม้ และยังประหยัดพลังงานและเป็นมิตรต่อสิ่งแวดล้อมอีกด้วย” เขาสรุปว่า “เราพบพันธมิตรที่มีความสามารถและตอบสนองความต้องการอย่างดีเยี่ยมใน GEW สำหรับใครก็ตามที่กำลังมองหาโซลูชัน UV สำหรับกาวร้อนละลาย ฉันขอแนะนำให้โทรติดต่อพวกเขา”
คลิกที่นี่เพื่อดูข้อมูลเพิ่มเติมเกี่ยวกับกระบวนการ UV เฉพาะทางของเรา